The Development of Metal Stamping Procedures: Advancements and Applications
The realm of steel stamping processes has actually witnessed a transformative journey noted by constant advancement and adjustment to fulfill the demands of contemporary commercial practices. The applications cover throughout a range of markets, each profiting distinctly from the developments in steel marking procedures.
Traditional Metal Stamping Strategies
Traditional metal stamping methods have long been the structure of manufacturing processes in different sectors due to their efficiency and precision. The process includes forming a metal sheet or coil into a preferred form by pushing it in between a die and a strike. This approach is extensively used for creating big quantities of get rid of high accuracy at a quick rate.
Among the key advantages of conventional metal stamping techniques is the ability to maintain tight tolerances, making certain that each component fulfills the called for requirements continually. This degree of accuracy is essential in markets such as auto, aerospace, and electronic devices, where also small variances can result in substantial concerns.
In addition, typical steel stamping techniques offer cost-effective options for mass production compared to various other producing methods. The capability to mark components in fast sequence lessens manufacturing time and minimizes labor costs, making it an attractive option for companies aiming to enhance their manufacturing procedures.
Introduction of High-Speed Stamping
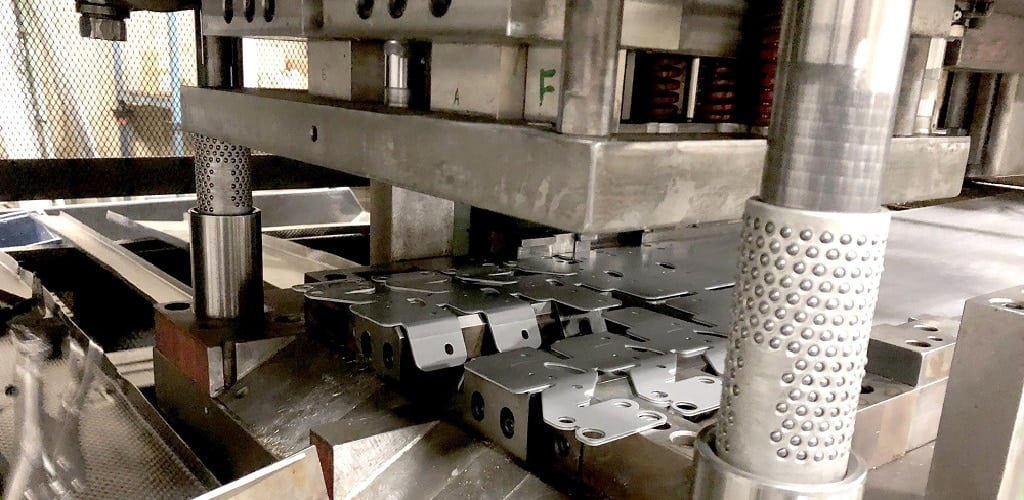
One of the vital benefits of high-speed stamping is its capability to keep precision and uniformity even at increased processing speeds. This precision is essential in industries where limited tolerances and complex designs are needed. Furthermore, high-speed marking allows for the handling of a vast array of products, including aluminum, stainless-steel, and copper, further broadening its applicability throughout various markets.
Furthermore, the development of high-speed marking has actually enabled view website makers to fulfill the growing demand for complicated parts in industries such as automobile, aerospace, and electronic devices (Metal Stamping). By leveraging the rate and accuracy of high-speed stamping innovation, business can boost their competition in a rapidly developing market landscape
Improvements in Tooling Technology
With the development of high-speed stamping allowing boosted accuracy and performance in steel forming processes, the field of metal stamping has seen considerable improvements in tooling innovation. Tooling modern technology plays a critical role in metal stamping procedures, affecting factors such as item top quality, manufacturing rate, and overall cost-effectiveness. One key development in tooling technology is the development of intelligent tooling systems that include sensing units and monitoring tools to provide real-time information on the marking procedure. These systems can discover problems such as tool wear or misalignment, allowing for prompt changes to keep ideal performance.
By using these innovative materials, tooling producers can generate passes away and molds that withstand the high pressures and temperature levels entailed in steel stamping processes, resulting in longer tool life and enhanced manufacturing effectiveness. On the whole, these developments in tooling innovation have actually changed the steel stamping industry, allowing makers to attain greater degrees of accuracy, performance, and cost savings.
Integration of Automation in Stamping
As automation proceeds to reshape the landscape of steel marking procedures, the assimilation of automated systems has actually come to be increasingly prevalent in modern-day manufacturing centers. Automated systems offer numerous advantages in steel marking, including enhanced effectiveness, enhanced accuracy, and enhanced safety. By incorporating automation right into marking procedures, suppliers can lower cycle times, decrease product waste, and enhance production throughput.
One of the vital elements of automation in stamping look at here is using robot arms for tasks such as product handling, part manipulation, and top quality assessment (Metal Stamping). These robotic systems can carry out repetitive and labor-intensive jobs with speed and accuracy, maximizing human drivers to concentrate on more complicated operations. Additionally, automation enables real-time monitoring and change of stamping procedures, resulting in greater overall procedure control and high quality guarantee
Moreover, the integration of automation in stamping allows manufacturers to attain consistent part top why not check here quality, meet tight resistances, and enhance general productivity. As innovation proceeds to development, the role of automation in steel marking processes is expected to increase further, driving advancement and efficiency in the manufacturing sector.
Applications Across Diverse Industries
Integrating metal marking processes throughout varied markets showcases the versatility and versatility of this manufacturing technique. In addition, the device market benefits from steel stamping processes to make parts for fridges, washing machines, and various other family appliances. The flexibility of metal stamping procedures makes it a useful manufacturing strategy across various markets, demonstrating its importance in modern-day production procedures.
Conclusion
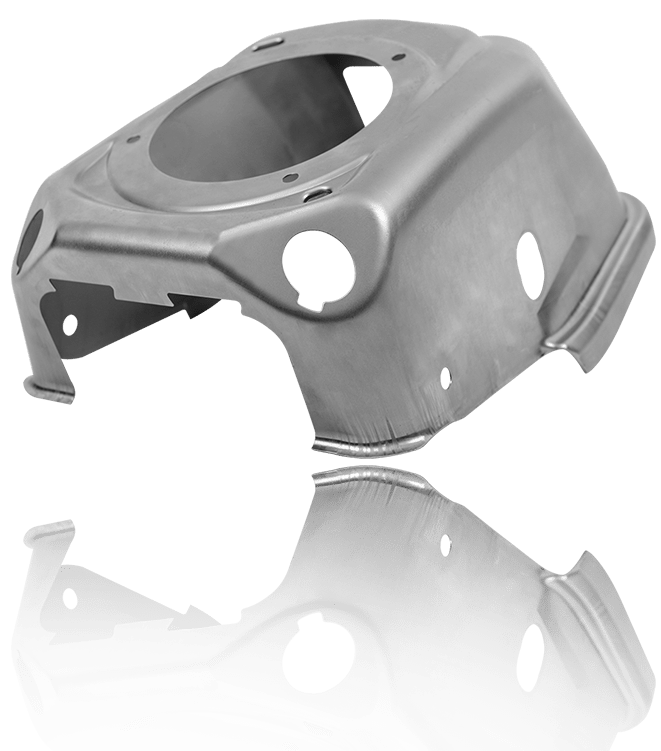